Réseaux sensibles au temps (TSN) : comment les normes IEEE contribuent à l’avènement de l’Industrie 4.0 en 5 points
Lors de mes déplacements aux quatre coins du monde, je rencontre des clients qui dépensent des centaines de milliers, parfois même des millions de dollars, pour concrétiser les promesses du concept Industrie 4.0. Ce nouveau modèle de connectivité omniprésente est une solide source d’inspiration pour les fabricants, qu’il s’agisse des plus grands équipementiers (OEM) de l’automatisation industrielle ou d’entreprises émergentes. Tous y voient la possibilité de gagner en productivité, en efficacité, en adaptabilité et, bien sûr, en rentabilité – que ce soit au niveau de leur résultat net, des employés, des partenaires ou des clients.
Le concept Industrie 4.0 promet un degré de flexibilité sans précédent qui augure d’une production agile en permettant, par exemple, aux fabricants de s’adapter à des besoins saisonniers ou à l’évolution des attentes des consommateurs. Il permettra ainsi d’allonger les périodes de disponibilité opérationnelle (avec une maîtrise accrue des frais généraux et des dépenses de maintenance), de réduire le temps et l’implication des ressources et d’accroître le niveau de confiance des entreprises et des clients. Ce ne sont là que quelques exemples des résultats qui devraient transformer l’industrie dans le cadre de la quatrième révolution industrielle.
La nécessité d’acquérir des données, de les échanger et de les analyser est au cœur même de cette formidable opportunité. Les données, et bien plus encore, les informations pertinentes que permet leur exploitation, sont la clé de ces nombreuses améliorations. Toutefois, dans la plupart des usines aujourd’hui, les données vivent dans des silos, isolées et inaccessibles – et donc sous exploitées. Pendant des années, les entreprises manufacturières ont essayé de résoudre ce problème, mais en raison de ce fonctionnement cloisonné, nombre de projets ont tourné court.
C’est dans ce contexte qu’apparaissent les réseaux sensibles au temps (TSN — Time Sensitive Network), un ensemble de normes Ethernet IEEE et dont le rôle est fondamental pour relever les nombreux défis de l’Industrie 4.0. Avec les réseaux TSN, toutes les données générées dans l’usine — de l’atelier aux serveurs en passant par le front office — peuvent cohabiter et communiquer. Première étape vers la suppression des silos de données qui entravent les communications industrielles, les réseaux TSN assurent un accès omniprésent à une mine de données dont la qualité facilitera la prise de décisions judicieuses. En résumé, les réseaux TSN sont le tremplin qui aidera les entreprises industrielles à concrétiser les promesses de l’Industrie 4.0 en s’appuyant sur cinq piliers dont la mission est de faciliter l’accès aux données.
- Création d’un langage commun — En uniformisant la synchronisation temporelle ainsi que le traitement global des paquets de données et des informations, les réseaux TSN permettent aux données de « parler » le même langage. Et même si des problèmes d’interopérabilité subsisteront entre les différents équipements, les fabricants pourront extraire davantage de valeur de leurs données, ces dernières empruntant désormais le même réseau Ethernet.
- Évolutivité et l’agilité — Les réseaux TSN peuvent aider le réseau Ethernet à gérer différents débits, de sorte que la bande passante disponible sera suffisante pour échanger les données, indépendamment de leurs niveaux de priorité respectifs. À terme, les fabricants pourront plus facilement moduler, à la hausse ou à la baisse, la capacité requise afin de s’adapter aux priorités et aux exigences de leurs clients.
- Une automatisation plus fiable — La technologie TSN prend en charge les données déterministes en temps réel qui jouent un rôle essentiel sur le plan de la précision. Si, pour une raison ou une autre, le timing d’un point de données (par exemple, un signal) est retardé ou décalé, une machine risque de ne pas répondre correctement, déclenchant un effet domino qui diminuera la productivité et provoquera des pertes financières. Imaginons le degré de précision requis pour qu’un robot travaille aux côtés d’un opérateur humain : si les mouvements du robot sont décalés ne serait-ce que d’une fraction de centimètre, la sécurité des opérateurs risque d’être compromise. Les réseaux TSN optimisent la communication instantanée de ce type d’applications pour améliorer, notamment, la sécurité et la qualité.
- Combler le fossé entre les spécialistes en technologies de l’information (IT) et ceux des technologies opérationnelles (OT) — En déployant un ensemble d’outils communs, la technologie TSN permet de répondre à la fois aux objectifs souvent distincts et concurrents des équipes informatiques (IT) et opérationnelles (OT). Elle crée un cadre commun où le langage partagé favorise la collaboration. En outre, de nombreux experts en technologies opérationnelles approchent de l’âge de la retraite, ce qui signifie que leur connaissance historique des bus de terrain actuels va disparaître. La technologie TSN a le potentiel pour combler ce manque de compétences à venir : il fournit un environnement commun où les spécialistes IT seront capables de gérer un environnement Ethernet industriel, avec à la clé des économies de ressources et une productivité en hausse.
- Affectation des investissements en R&D à d’autres postes — Dans la mesure où la technologie TSN résout les contraintes de bande passante, les entreprises qui souhaitent augmenter leur débit ou ajouter des capacités n’ont plus besoin de définir de nouvelles allocations de bande passante. Les exemples d’entreprises ayant investi des millions de dollars dans des infrastructures obsolètes ou devenues inefficaces une dizaine d’années plus tard ne manquent pas. En limitant sensiblement la nécessité de reconstruire l’infrastructure requise, les réseaux TSN dégagent des opportunités d’investissement au profit de technologies qui favorisent l’automatisation ; des capitaux pourront par exemple être réinvestis dans la formation d’employés qui apprendront à gérer et exploiter des systèmes robotisés d’une grande complexité.
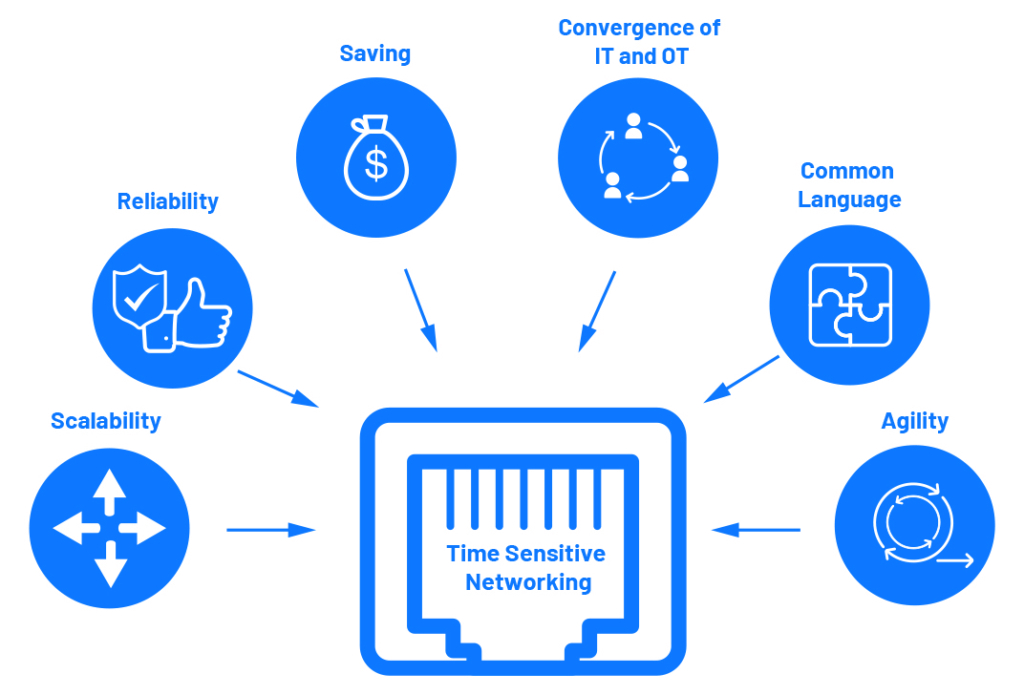
Conclusion
Il ne fait aucun doute que les normes TSN représentent un atout crucial pour l’Industrie 4.0 et les nombreuses applications que ce concept va transformer, ouvrant la voie à une nouvelle génération de technologies qui révolutionneront le mode de fonctionnement des fabricants. Ce n’est, pour le moment, qu’un pan d’un vaste écosystème que nous construisons pour donner vie à la quatrième révolution industrielle. Cette approche requiert des logiciels, des middleware, des composants microélectroniques avancés, de brillants inventeurs et ingénieurs, des techniciens et des opérateurs dédiés, de la formation et du temps. Mes collègues d’Analog Devices et de toute l’industrie sont convaincus par l’extraordinaire potentiel que recèlent ces technologies émergentes. De même que nos clients et partenaires, tous voient dans cette opportunité quasiment illimitée une formidable source d’inspiration.
Analog Devices propose un portefeuille de solutions Ethernet TSN qui contribuent à l’avènement de l’Industrie 4.0. Pour de plus amples informations sur le portefeuille ADI Chronous et sur la manière dont il accélère la transition vers les réseaux Ethernet industriels dans le monde réel, consulter le site analog.com/chronous.
Pourquoi Schneider Electric fait de la fabrication additive un fer de lance
Chez Schneider Electric, l’industrie du futur, ou industrie 4.0, se fait à grande échelle, à travers l’ensemble de ses activités mondiales, et prend le nom de « Smart Factory ». Cela passe bien sûr par l’Internet industriel des objets (IIoT) et globalement la transformation digitale, mais pas seulement. Dans l’usine de Puente la Reina, en Espagne, la stratégie repose quant à elle sur l’adoption de la fabrication additive FDM (Fused Filament Fabrication) pour l’ensemble de son processus de production.
Pour le groupe, l’expérience est plus que positive puisque celui-ci affirme avoir beaucoup gagné en efficacité, notamment au niveau de ses opérations d’outillage… au point que l’usine de Puente la Reina s’est récemment vue attribuer le prix « Smart Factory » décerné à l’échelon européen par Schneider Electric en reconnaissance de l’accélération de son processus de transformation Industrie 4.0. Un grand nombre d’outils de fabrication est en effet imprimé en 3D et des économies considérables en temps et en argent ont ainsi été obtenues, sans compter l’amélioration de la chaîne d’approvisionnement.
Moins de dépendance vis-à-vis des fournisseurs
« En 2019, avec l’utilisation de la fabrication additive FDM de Stratasys, nous avons économisé près de 20 000 € rien que dans la réalisation de l’outillage de la chaîne de montage, ce qui a largement compensé notre investissement initial dans l’imprimante 3D F170, détaille Manuel Otamendi, responsable de l’industrialisation et de la maintenance de la chaîne d’approvisionnement mondiale de l’usine de Schneider Electric à Puente la Reina. Grâce à cette technologie, nous sommes en mesure de réaliser de nouveaux outils de production à hautes performances en une seule journée, alors qu’auparavant, il nous aurait fallu sous-traiter leur fabrication et attendre au moins une semaine ».
Le responsable industrialisation et maintenance ajoute avoir également réduit considérablement sa dépendance vis-à-vis des fournisseurs et une meilleure maîtrise de la production des outils, « ce qui se traduit par une amélioration de la flexibilité de l’ensemble de notre processus de fabrication et une diminution des délais de commercialisation de nombreux produits. »
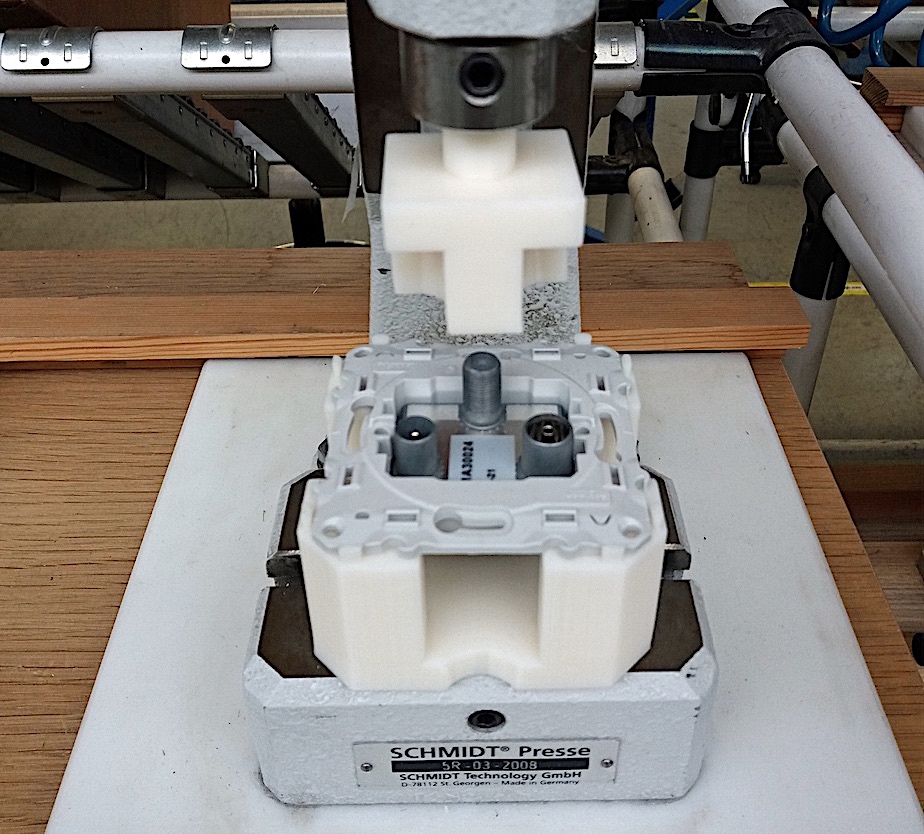
Une utilisation étendue de la fabrication additive
L’usine espagnole de Schneider Electric a recours à l’imprimante 3D F170 dans un large éventail d’applications d’outillage, notamment pour la réalisation d’outils, de gabarits, de fixations, de bras préhenseurs et autres outils robotiques pour les chaînes de montage. Auparavant, la fabrication de tous ces éléments était sous-traitée à des tiers qui utilisaient des processus de moulage par injection ou d’usinage CNC. Devenue un véritable cheval de bataille pour l’usine de Puente la Reina, la machine réalise plus d’une centaine de nouveaux outils de production chaque année. Exemple d’application : la production de préhenseurs de bras robotiques pour la chaîne de montage. Grâce à son imprimante 3D F170, Schneider Electric a pu développer de nouvelles idées pour les préhenseurs, qui lui ont permis d’améliorer les performances de ses robots et de faire encore plus d’économies. « L’externalisation d’un préhenseur usiné nous coûtait 200 euros par outil, précise Manuel Otamendi. Aujourd’hui, nous pouvons les imprimer en 3D à la demande, pour environ 100 euros chacun. La possibilité de simplifier notre chaîne d’approvisionnement est également très importante pour nous aujourd’hui. Pour cela, il est essentiel de disposer de cette capacité à fabriquer les pièces à la demande en interne. » Et c’est sans compter l’effet positif sur l’efficacité de l’ensemble de l’usine et la réduction des délais de commercialisation. Des atouts non négligeables, en particulier en temps de crise, période qui a la fâcheuse tendance à compresser les coûts et les délais…
« Grâce à la technologie de fabrication additive FDM, nous sommes en mesure de réaliser de nouveaux outils de production à hautes performances en une seule journée, alors qu’auparavant, il nous aurait fallu sous-traiter leur fabrication et attendre au moins une semaine » – Manuel Otamendi, responsable de l’industrialisation et de la maintenance au sein de l’usine Schneider Electric de Puente la Reina.
Plongée au cœur de l’usine 4.0 d’ifm electronic
« 69, année électronique »… aurait pu chanter le « Serge Gainsbourg de l’industrie » s’il avait existé. Car cette année-là accoucha d’un des plus grands spécialistes mondiaux des capteurs, des contrôleurs et des systèmes pour l’automatisation industrielle dans le monde entier. Aujourd’hui, ifm electronic est dirigé par la deuxième génération de la famille ; co-fondé Robert Buck et Gerd Marhofer, le groupe est aujourd’hui mené par le président du directoire Martin Buck et Michael Marhofer. Avec environ 6 700 employés répartis dans pas moins de soixante-dix pays, ifm combine l’internationalité et la force d’innovation d’un groupe (qui compte pas moins d’un millier de personnes en R&D) d’entreprises en pleine croissance – formé de nombreuses acquisitions externes – mais aussi en s’engouffrant habilement dans la brèche de l’industrie 4.0.
L’usine de Tettnang d’ifm montre à elle-seule comment utiliser Industry 4.0 avec succès. L’exemple de la surveillance des filtres dans la production de capteurs illustre les avantages de la maintenance calibrée à partir de l’état de santé de l’équipement et son suivi en temps réel, et ce grâce au recours massif de capteurs communicants IO-Link d’ifm ainsi que la solution SmartObserver LR. Pour Laurent Carlion, directeur marketing et technique de la filiale française, « l’industrie du futur s’illustre avant tout par le rapprochement de l’IT et de l’outil en lui-même, car bien souvent, la production reste trop détachée du reste de l’entreprise ; il n’existe donc pas ou très peu de relations entre les services. L’industrie 4.0 vise au contraire à rapprocher ces deux univers, sans oublier la maintenance et l’automatisation des flux. »
On n’est jamais mieux servi que par soi-même
L’illustration parfaite dans cette usine de Tettnang dans laquelle ifm a mené une approche s’appuyant sur des sous-projets réalisés au niveau des machines et des postes de travail de la production électronique où s’y trouvent de nombreuses unités d’extraction reliées à un système d’extraction central par des tuyaux. Les filtres retenant la poussière et les particules sont installés sur le système d’extraction central et sur les différentes unités d’extraction décentralisées ; or si les filtres sont trop encrassés, le débit d’air diminue et le fonctionnement fiable de la machine n’est pas assuré, d’où un entretien de l’équipement indispensable. Dans le passé, les filtres étaient remplacés à des intervalles de maintenance réguliers. Problème de la maintenance préventive, les filtres étaient souvent remplacés soit trop tôt, soit trop tard.
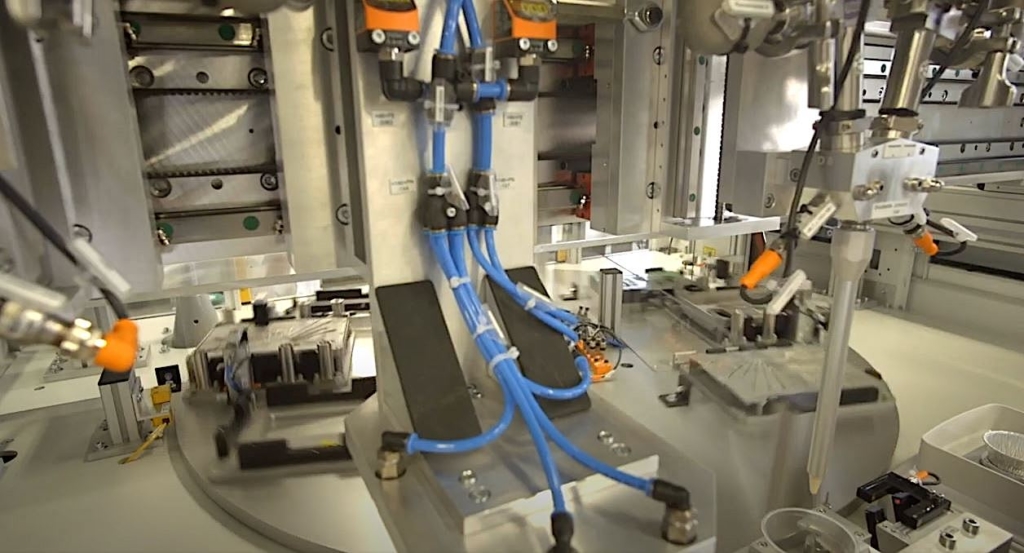
Dans le cadre d’un projet d’industrie 4.0, le système a été modifié pour une maintenance basée sur l’état. Le degré de contamination des filtres a été mesuré en permanence afin de déterminer le moment optimal pour l’entretien. Des compteurs d’air comprimé, de type SD0523, ont été installés sur les filtres décentralisés connectés à un module maître IO-Link, de type AL1302. Pour évaluer les valeurs mesurées par les capteurs de débit, le système LineRecorder d’ifm est utilisé – cette solution assure les différentes étapes, de la collecte et la consolidation des données de terrain, à la transmission des données, en passant par l’évaluation, l’analyse et la visualisation de celles-ci. Le système se compose de différents outils logiciels permettant une transmission simple des données des différents capteurs vers des systèmes de niveau supérieur. Le module maître IO-Link fonctionne avec le noyau IoT qui fournit les valeurs du processus. L’évaluation est effectuée dans le SmartObserver LR de niveau supérieur. L’interface utilisateur basée sur le Web LR SmartObserver Cockpit permet d’afficher les valeurs mesurées, de définir les limites et de configurer la gestion des alarmes. Grâce à une connexion au système SFI (Shop Floor Integration), les ordres de maintenance sont directement déclenchés dans le système SAP en cas de dépassement des limites.
Dans le passé, les filtres étaient remplacés à des intervalles de maintenance réguliers. Problème de la maintenance préventive, les filtres étaient souvent remplacés soit trop tôt, soit trop tard.
Un exemple progressivement adopté dans les usines françaises
En somme, de la maintenance conditionnelle, dont le but est de faire correspondre l’ensemble des flux quand apparaît une panne, avec une remontée d’informations vers le système informatique ou l’ERP de l’entreprise, on est passé à la maintenance prévisionnelle. « Mais il reste du chemin à parcourir car toutes les étapes de la maintenance conditionnelle peuvent aujourd’hui être automatisées, même si l’on constate en France un changement des mentalités au sein des entreprises ». Exemple ? La solution d’analyse vibratoire que la société a mise au point il y a plus de dix ans et permettant de faire de la maintenance conditionnelle sans faire appel à un expert ; l’allemand a constaté peu de retours durant cette décennie en raison du fait que « les gens n’étaient pas prêts. Mais avec l’industrie 4.0, d’un seul coup, la demande a explosé depuis trois ans. On a même revu notre organisation française avec une personne entièrement dédiée à cette solution ».
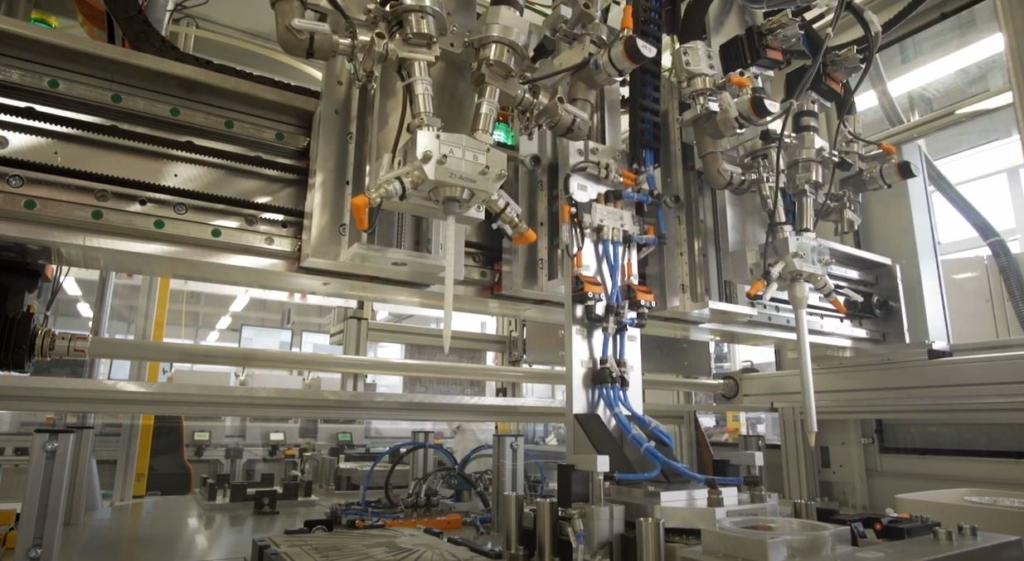
Selon Laurent Carlion, « la France a même repris goût à l’industrie et les investissements vont dans le sens de l’amélioration du parc machines qui, il faut bien le reconnaître, est un peu plus âgé qu’ailleurs. » au regard de la crise dramatique nous subissons traversons actuellement, numériser et monitorer tous ces parcs de machines vieillissante ne se révèlent plus seulement utiles mais s’imposent parfois comme une question de survie de l’entreprise. Certes, les propos datent d’avant la crise… mais le « monde d’après » devrait logiquement poursuivre cette tendance.
Il y a plus de dix ans, ifm a mis au point une solution d’analyse vibratoire permettant de faire de la maintenance conditionnelle sans faire appel à un expert. L’entreprise a constaté peu de retours durant cette décennie car « les gens n’étaient pas prêts. Mais avec l’industrie 4.0, d’un seul coup, la demande a explosé depuis trois ans. »
Vers des solutions de gestion de stocks plus automatisées
Dans le contexte douloureux que les entreprises traversent, si celles-ci doivent tout faire pour remettre leur production en route et stimuler la demande, elles devront dès que possible investir dans les nouvelles technologies, à commencer par des solutions d’intralogistiques visant à fluidifier les flux de production et optimiser la gestion des magasins de pièces de rechange.
C’est du moins l’avis de William Fleuriot, directeur commercial de la filiale française de SSI Schaefer, spécialiste allemand de l’intralogistique – allant du simple bac à boulons aux solutions les plus complexes et automatisées ; « avant la crise, l’industrie était déjà tournée vers des solutions automatisées dans le but de servir des clients de façon plus rapide et plus précise, en réduisant au maximum le nombre d’erreurs ».
En matière de solution pour la gestion des pièces détachées et des pièces de rechange, le principal sujet de réflexion tourne toujours autour de la volumétrie. C’est à partir de celle-ci que l’on détermine ses besoins ; « chez Schaefer, on analyse la volumétrie et le niveau d’exigence en matière de performance attendues avant de proposer la moindre solution. Nos systèmes vont de l’organisation des zones de préparation de stockage avec des systèmes de rayonnages palettes par exemple, à des solutions plus automatisées visant à optimiser les flux et à réduire les déplacements des préparateurs de commande. En outre, certains de nos clients désirent ensuite monter en gamme avec une armoire automatique dotée de convoyeurs mécanisés et, en bout de chaîne, un système d’emballage et d’expédition automatisé ». Chose est sûre pour le directeur commercial, « seules les entreprises disposant d’une logistique performante et d’une gestion des flux 2.0 ont pu tirer leur épingle du jeu ».
En cela, la gestion des pièces détachées demeure un élément déterminant en ces temps de crise mais aussi pour répondre à des marchés de plus en plus exigeants. Car ces dernières années, les industriels n’ont cessé de réduire leurs stocks. Aujourd’hui, l’heure est à l’automatisation dans la mesure où celle-ci permettra sans nul doute, combinée à d’autres solutions d’industrie 4.0, de gagner des parts de marché en augmentant les volumes de ventes et en réduisant les erreurs de préparation de commande. « N’oublions pas qu’optimiser l’outil de production permettra inévitablement de grossir les marges, ce qui demeure, y compris après la crise, le nerf de la guerre ».
Même en temps de crise, le format des Sepem continuent de séduire les industriels
Quel regard portez-vous sur la crise ?
Philippe Dutheil : Sans surprise, l’événementiel a été particulièrement touché avec l’annulation de nombreux événements et le report à 2021 des salons internationaux. Du côté de nos exposants, la crise a été essentiellement sanitaire, en particulier dans le Grand Est, puis économique avec la fermeture de la quasi-totalité des entreprises durant deux mois. Si de ce point de vue l’impact a été, en Alsace et en Lorraine notamment, similaire au reste de la France, nous constatons que dans cette région plus rigoureuse que d’autres, la population et les entreprises savent parfaitement s’adapter aux contraintes sanitaires, de confinement et au geste barrière avec une volonté de rapidement s’en sortir.
Xavier Legrand : Concernant le salon Sepem, si en Alsace l’automobile est très présente, les secteurs comme la cosmétique, la pharmaceutique et l’agroalimentaire représentent aussi des parts importantes dans le tissu industriel de la région. Il en est de même pour le sud-est de la France, ce qui ne devrait donc pas trop impacter nos salons par rapport à d’autres événements beaucoup plus orientés vers l’automobile et l’aéronautique.
Avant même de parler de Colmar, comment se présente l’édition du sud est qui aura lieu à Avignon à la rentrée ?
Philippe Dutheil : Contrairement à Colmar, l’édition avignonnaise a été maintenue aux mêmes dates, à savoir du mardi 29 septembre au jeudi 1er octobre. Ce salon Sepem aura la particularité, comme à Grenoble en février dernier, de se dérouler conjointement avec le Forum de l’Électronique, également organisé par le groupe GL Events. Compte tenu de la situation actuelle, nous avons choisi d’adapter raisonnablement la surface afin de libérer de l’espace et de ne pas trop resserrer les stands ; dans tous les cas, le porterons une vigilance de tous les instants d’un point de vue sanitaire et les gestes barrières seront régulièrement rappelés. De même, les deux événements seront rassemblés au sein d’un seul et même hall d’exposition. Il n’y aura donc pas d’extension mais plutôt une petite diminution en raison de la crise. Toutefois, à la mi-mai, nous enregistrons déjà un taux de remplissage à 80 % ; celui-ci devrait encore augmenter d’ici là.
Xavier Legrand : Au niveau des temps forts, le cycle de conférences sur la maintenance – dont les thèmes seront également élargis aux process de production – sera maintenu mais il sera exceptionnellement allégé et organisé conjointement aux conférences de l’électronique. Concrètement, les conférences sur la maintenance se dérouleront les mardi, mercredi et jeudi matin ; celle portant sur l’électronique se dérouleront les mardi et mercredi après-midi.
Malgré son report, comment se présente l’édition de Colmar ?
Philippe Dutheil : Au printemps, la commercialisation était déjà terminée et le salon affichait déjà complet. À ce jour, malgré quelques demandes d’annulation faites par les entreprises pour récupérer du cash, nous enregistrons peu de pertes. Nous remarquons également qu’au second semestre de cette année, les nombreux salons et événements qui auront lieu à cette période vont pousser les entreprises à faire des choix ; dans ce contexte, les Sepem présentent l’avantage d’être peu onéreux avec des petits stands et des retours sur investissement rapides. À ce titre, nous restons relativement sereins.
Votre sentiment pour 2021 ?
Xavier Legrand : Pour le moment, notre seul repère, c’est l’édition de Douai. À l’heure actuelle, nous enregistrons très peu de pertes et nous sommes donc très confiants ; nous avons donc la volonté de travailler sur une surface identique d’autant qu’il s’agit d’un gros salon pour nous.
Philippe Dutheil : Tout à fait, et c’est là qu’on voit que l’alchimie des Sepem (avec le prix des achats plus bas et donc moins de risque sur l’investissement ainsi que des temps de déplacement réduits) continue de séduire les exposants. Pour autant, nous ne nous faisons pas d’illusion : 2021 sera également une année difficile.
L’Alsace accueillera une usine Dräger de production de masques de protection de type FFP2/FFP3
Cette information tombée le 16 juin dernier est à double titre une bonne nouvelle. Celle-ci répond en effet à deux priorités exprimées de plus en plus fortement par Bruno Le Maire depuis la crise du coronavirus : la première (qui l’est déjà depuis plusieurs années) est d’attirer sur notre territoire des investissements étrangers, à plus forte raison de nature industrielle ; la seconde consiste à renforcer notre capacité de production de matériels de protection individuelle et vitale.
Et la secrétaire d’Etat Agnès Pannier-Runacher ne cache pas son enthousiasme, forte des récents – et très bons – chiffres de la France en matière d’attractivité : « Les autorités françaises accueillent avec un grand intérêt ce projet destiné à servir non seulement le marché français, mais également européen. Il vient conforter la stratégie d’attractivité que nous déployons depuis plusieurs années et qui a vu la France se positionner à la première marche du classement des investissements étrangers en Europe en 2019 ».
Cet investissement viendra renforcer l’empreinte en France de Dräger, entreprise familiale allemande de 2,8Md€ de chiffre d’affaires et 14 000 employés (tout de même !) et spécialisée dans le domaine des technologies médicales et de sécurité. « Nous avons été accompagnés dans nos réflexions par les autorités françaises et les équipes de Business France dès le début de notre projet, a indiqué Yves Le Gouguec, président de Dräger France. Le département du Bas-Rhin et la région Grand Est ont affiché, au travers de l’Agence de développement d’Alsace (Adira), une détermination sans faille pour accueillir cet investissement ». Si le lieu exact et la date de construction n’a pas encore été dévoilé, l’usine devrait voir le jour dans les mois à venir, d’ici la fin de l’année.
Comment PTC a adapté les nouvelles technologies à la crise sanitaire
Entre pandémie, crise économique et télétravail, comment vos clients vivent-ils la situation actuelle ?
Nous rencontrons trois cas de figure : les entreprises qui ont purement et simplement fermé leurs portes durant le confinement, celles qui ont suspendu leurs investissements et celles qui ont pu travailler à distance et adapter la production. D’autres sont également à la recherche de solutions spécifiques comme pour les services de maintenance qui souhaitent donner la priorité au support technique ou encore ceux qui ont répondu aux appels du ministre de la Santé… Toutes ces entreprises ont eu un besoin urgent de former leurs équipes rapidement et de calibrer leurs lignes de production.
Quelles solutions leur proposez-vous ?
Tout d’abord, la solution la plus utilisée se nomme Chalk, le « FaceTime » de la réalité augmentée. Il s’agit d’une application disponible dans l’App Store permettant de scanner l’environnement de travail et de se connecter à distance. L’objectif étant de pouvoir dépanner une ligne de production ou une machine sans avoir besoin d’envoyer un technicien sur place. Cet outil va nous permettre d’accélérer la transformation digitale en cours des entreprises qui auront choisi d’adopter ce mode opératoire. Cette technologie illustre un inversement de tendance dans les usages puisqu’elle sera désormais utilisée en priorité. De nombreuses applications sont potentiellement à venir dans l’industrie mais également dans le monde du transport ferroviaire qui exige, lorsqu’une locomotive tombe en panne, l’intervention d’une équipe sur place se déplaçant avec un train de secours.
Vuforia Expert Capture est une technologie de réalité augmentée permettant également d’intervenir à distance en capturant le savoir-faire d’un expert avant de le scénariser via une tablette ou un smartphone. Il s’agit d’un outil d’e-learning à part entière qui prend tout son sens dans cette crise puisqu’un expert peut ainsi transférer son savoir-faire dans n’importe quel pays sans se déplacer.
Qu’est-ce que le Covid-19 va changer dans la prévention des risques, la formation et la maintenance ?
Beaucoup d’entreprises, en particulier des grands comptes, n’étaient pas calibrés pour travailler à distance ni pour piloter la maintenance. Il faut désormais qu’ils durcissent leur système informatique en matière de sécurité et le rendent accessible au plus grand nombre – à commencer par les ingénieurs – avec des solutions Cloud, SaaS et PLM. La crise que nous traversons posent inévitablement ces questions.
Victime d’une cyberattaque, le groupe Schmersal reprend ses activités
« Notre téléphone a sonné le 20 mai à 16h45 : le groupe Schmersal a officiellement été informé que des cybercriminels préparaient une attaque ciblée sur le réseau de l’entreprise, relate-t-on au sein du groupe allemand. En l’espace de 90 minutes, le système informatique complet était déconnecté dans le monde entier. Plus rien ne fonctionnait : du central téléphonique à toute l’infrastructure du système ERP et de la production complète à l’entrepôt entièrement automatisé, sur tous les sites ».
Le groupe indique toutefois que ses experts en informatique légale étaient parvenus à identifier et isoler le logiciel malveillant mais, par précaution, les systèmes sont rester désactivés jusqu’à ce qu’ils puissent être définitivement nettoyés plusieurs jours durant. Pendant cette période d’arrêt de production complet, le service administratif et le service commercial ont informé les clients, les fournisseurs et les autres partenaires commerciaux.
Une protection standard impuissante contre les attaques ciblées
Pour Philip Schmersal, « de telles situations montrent à quel point une entreprise dépend aujourd’hui des technologies de l’information. Nous avons donc déployé de grands efforts pour contacter nos clients et les tenir au courant de toutes les manières imaginables. Après tout, nous souhaitions limiter au minimum les perturbations des chaînes d’approvisionnement de nos clients. » L’associé et gérant du groupe n’a d’ailleurs pas manqué de saluer « l’engagement du personnel qui, indépendamment de ses horaires de travail et de son appartenance à un service, a maintenu un service d’urgence sans réseau d’entreprise, même pendant le week-end », ainsi que les entreprises voisines. En ces temps de crise, qui a comme l’illustre cet exemple permis aux cybercriminels de multiplier des attaques, la solidarité est de mise.
L’attaque a surtout montré que la protection standard habituelle avec des programmes antivirus et des pare-feux est impuissante contre les attaques ciblées avec des logiciels malveillants jusqu’alors inconnus. Schmersal a immédiatement mis à disposition des grands fournisseurs de programmes antivirus des informations concernant ce logiciel malveillant. Les fournisseurs ont étendu leur protection en conséquence, de sorte que ce virus ne puisse très probablement plus causer de dommages. Philip Schmersal : « Nous avons cependant appris que l’informatique des petites et moyennes entreprises doit se redéfinir – et à quelle vitesse le thème de la « sécurité » devient prioritaire. »
« De telles situations montrent à quel point une entreprise dépend aujourd’hui des technologies de l’information. Nous avons donc déployé de grands efforts pour contacter nos clients et les tenir au courant de toutes les manières imaginables »
Philip Schmersal
La lubrification automatique, fer de lance de la productivité
À quels secteurs d’activite appartiennent vos clients ?
Notre matériel s’adresse à tous les secteurs d’activité. Dès lors que des pièces sont en mouvement une lubrification s’impose afin de prolonger la durée de vie des éléments.
Quelles sont leurs problématiques en matière de graissage et de lubrification ?
Les machines et les installations doivent pouvoir fonctionner parfaitement dans toutes sortes de conditions plus ou moins extrêmes. L’humidité, la température, les fortes charges, l’utilisation intensive, l’ambiance corrosive et/ou abrasive, l’accessibilité difficile ou dangereuse sont autant de paramètres/facteurs qui peuvent affecter considérablement la durée de vie des roulements, des chaines, des engrenages, des guidages linéaires, des glissières et entrainer une défaillance lourde de conséquence pour la production.
Quelle solution leur proposez-vous ?
Nous proposons une large gamme de graisseurs, disponibles en 5 contenances (15, 30, 60, 125 et 250 ml) ainsi qu’une version multi-points (5 x 8 ml) accompagnée d’une grande palette d’accessoires pour des montages déportés avec ou sans dont un amplificateur de pression. Nous répondons également à toutes les règlementations en vigueur du fait de notre partenariat avec les plus grands fabricants de lubrifiants. (Exemple : Nos lubrifiants de qualité alimentaire sont certifiés NSF H1). Les graisseurs Simatec peuvent être montés dans toutes les positions, sous l’eau (IP68) y compris en atmosphère potentiellement explosive (Atex).
En cette période de crise économique, en quoi un bon graissage permet-t-il de gagner en productivité ?
La lubrification automatique continue permet un apport régulier en lubrifiant et évite ainsi les phases de lubrification excessives puis insuffisantes nuisibles aux pièces mécaniques en mouvement pouvant ainsi engendrer des détériorations prématurées. La lubrification automatique fiabilise ainsi les équipements de production, évite les arrêts de production inutiles et permet également un gain de temps considérable par rapport à une solution de graissage manuel. Ce gain de temps permet d’affecter les ressources à des tâches à plus forte valeur ajoutée. Enfin, Il est à noter qu’il est possible d’effectuer trois remplissages supplémentaires avant remplacement du graisseur réduisant ainsi les coûts d’approvisionnement, permettant également l’utilisation d’un lubrifiant spécifique.
Bleam aide Total à digitaliser la surveillance de ses installations
Dans le cadre de son programme Total Industrial Mobility (TIM), dirigé par François Dalémat et chargé de doter les intervenants des différents sites du groupe des outils de mobilité simples afin de mieux interagir sur le terrain et améliorer la sécurité, Total s’est appuyé sur les compétences de la start-up française Ubleam et sa solution Bleam. Ce logo intelligent est capable de connecter les objets pour en délivrer un contenu interactif. Il scanne des objets à plus de 4 m. de distance et ce dans des environnements atypiques en supportant la déformation et en s’adaptant aux formes souples et aux courbes. « Notre solution est particulièrement ergonomique et intuitive, ajoute Samuel Boury, co-fondateur d’Ubleam. Avec le Bleam, nous pouvons également envoyer des données vers une interface de réalité augmentée ».
Total a sollicité la start-up pour réaliser des premiers prototypes d’application sur la raffinerie de Donges, près de Nantes ; « sur ce site sont installées des systèmes de fuite temporaire, des équipements permettant d’éviter les fuites dans le réseau. Celles-ci sont très nombreuses et difficiles à suivre, précise François Dalémat. Les tags intelligents et industriels d’Ubleam, robustes à la lecture et capables d’être lus de loin en pouvant être grossis 50 fois, de biais et en trois dimensions – sur des tuyaux par exemple, nous avons été séduits par les premiers prototypes ».
Les applications sont diverses et variées ; elles vont des opérations de maintenance aux simples tournées en passant par le suivi, l’identification et le tracking d’équipements tels que les soupapes de sécurité, soit des centaines d’éléments de petite taille mais indispensables au démarrage d’une raffinerie. Le Bleam sert aussi à s’assurer qu’on intervient sur le bon équipement, au bon endroit et enrichit l’expérience utilisateur. Il est également possible de faire de la reconnaissance de forme afin de savoir, grâce au tag, si une vanne est ouverte ou fermée. Mais l’application prioritaire demeure l’amélioration de la sécurité et la productivité. Dans le cas d’une fuite vapeur, avec le tag d’Ubleam il est possible d’identifier instantanément le problème, de prendre une photo, d’enrichir avec des informations nécessaires avant de tout envoyer à l’ERP ainsi qu’à d’autres logiciels « compétents ».
Les tags intelligents et industriels d’Ubleam sont robustes à la lecture et capables d’être lus de loin en pouvant être grossis 50 fois, de biais et en trois dimensions