Pourquoi Schneider Electric fait de la fabrication additive un fer de lance
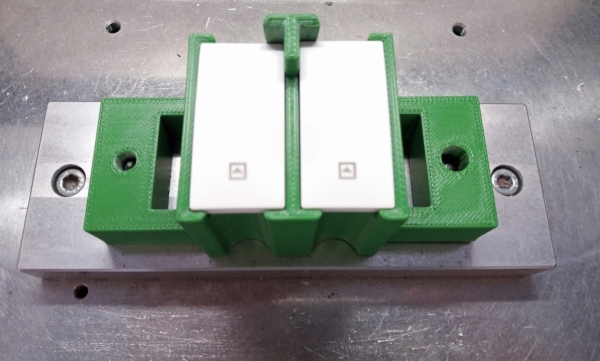
Chez Schneider Electric, l’industrie du futur, ou industrie 4.0, se fait à grande échelle, à travers l’ensemble de ses activités mondiales, et prend le nom de « Smart Factory ». Cela passe bien sûr par l’Internet industriel des objets (IIoT) et globalement la transformation digitale, mais pas seulement. Dans l’usine de Puente la Reina, en Espagne, la stratégie repose quant à elle sur l’adoption de la fabrication additive FDM (Fused Filament Fabrication) pour l’ensemble de son processus de production.
Pour le groupe, l’expérience est plus que positive puisque celui-ci affirme avoir beaucoup gagné en efficacité, notamment au niveau de ses opérations d’outillage… au point que l’usine de Puente la Reina s’est récemment vue attribuer le prix « Smart Factory » décerné à l’échelon européen par Schneider Electric en reconnaissance de l’accélération de son processus de transformation Industrie 4.0. Un grand nombre d’outils de fabrication est en effet imprimé en 3D et des économies considérables en temps et en argent ont ainsi été obtenues, sans compter l’amélioration de la chaîne d’approvisionnement.
Moins de dépendance vis-à-vis des fournisseurs
« En 2019, avec l’utilisation de la fabrication additive FDM de Stratasys, nous avons économisé près de 20 000 € rien que dans la réalisation de l’outillage de la chaîne de montage, ce qui a largement compensé notre investissement initial dans l’imprimante 3D F170, détaille Manuel Otamendi, responsable de l’industrialisation et de la maintenance de la chaîne d’approvisionnement mondiale de l’usine de Schneider Electric à Puente la Reina. Grâce à cette technologie, nous sommes en mesure de réaliser de nouveaux outils de production à hautes performances en une seule journée, alors qu’auparavant, il nous aurait fallu sous-traiter leur fabrication et attendre au moins une semaine ».
Le responsable industrialisation et maintenance ajoute avoir également réduit considérablement sa dépendance vis-à-vis des fournisseurs et une meilleure maîtrise de la production des outils, « ce qui se traduit par une amélioration de la flexibilité de l’ensemble de notre processus de fabrication et une diminution des délais de commercialisation de nombreux produits. »
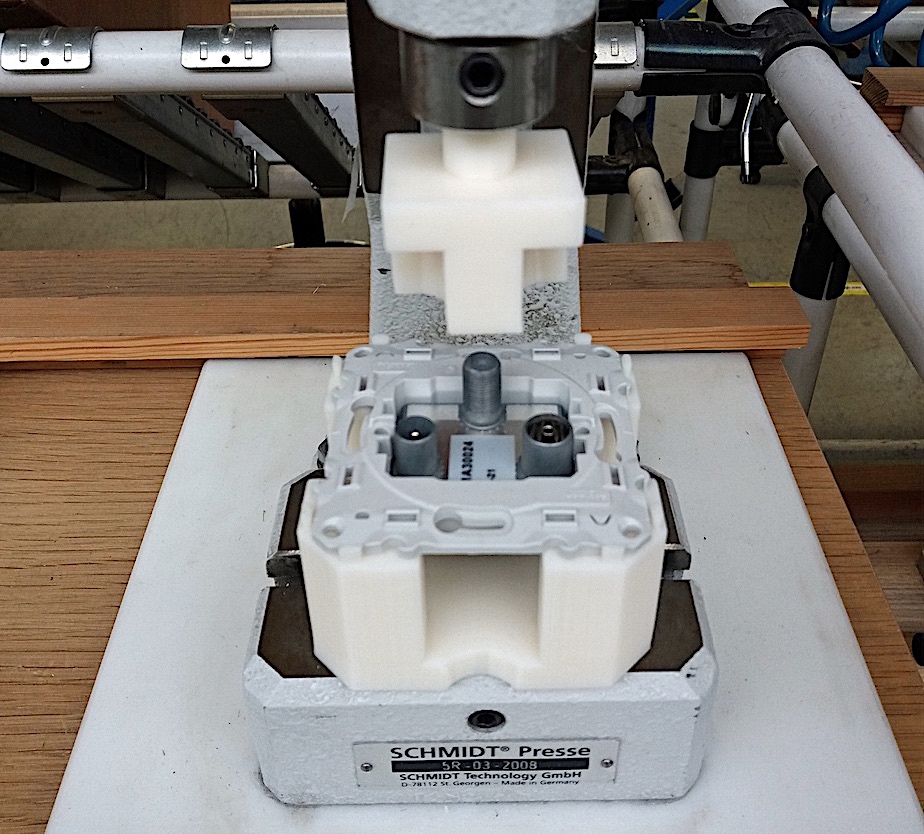
Une utilisation étendue de la fabrication additive
L’usine espagnole de Schneider Electric a recours à l’imprimante 3D F170 dans un large éventail d’applications d’outillage, notamment pour la réalisation d’outils, de gabarits, de fixations, de bras préhenseurs et autres outils robotiques pour les chaînes de montage. Auparavant, la fabrication de tous ces éléments était sous-traitée à des tiers qui utilisaient des processus de moulage par injection ou d’usinage CNC. Devenue un véritable cheval de bataille pour l’usine de Puente la Reina, la machine réalise plus d’une centaine de nouveaux outils de production chaque année. Exemple d’application : la production de préhenseurs de bras robotiques pour la chaîne de montage. Grâce à son imprimante 3D F170, Schneider Electric a pu développer de nouvelles idées pour les préhenseurs, qui lui ont permis d’améliorer les performances de ses robots et de faire encore plus d’économies. « L’externalisation d’un préhenseur usiné nous coûtait 200 euros par outil, précise Manuel Otamendi. Aujourd’hui, nous pouvons les imprimer en 3D à la demande, pour environ 100 euros chacun. La possibilité de simplifier notre chaîne d’approvisionnement est également très importante pour nous aujourd’hui. Pour cela, il est essentiel de disposer de cette capacité à fabriquer les pièces à la demande en interne. » Et c’est sans compter l’effet positif sur l’efficacité de l’ensemble de l’usine et la réduction des délais de commercialisation. Des atouts non négligeables, en particulier en temps de crise, période qui a la fâcheuse tendance à compresser les coûts et les délais…
« Grâce à la technologie de fabrication additive FDM, nous sommes en mesure de réaliser de nouveaux outils de production à hautes performances en une seule journée, alors qu’auparavant, il nous aurait fallu sous-traiter leur fabrication et attendre au moins une semaine » – Manuel Otamendi, responsable de l’industrialisation et de la maintenance au sein de l’usine Schneider Electric de Puente la Reina.
Partenariat entre RS France et Afim pour faciliter l’accès à des solutions de maintenance de nouvelle génération
Dans le cadre d’une initiative stratégique visant à proposer des solutions innovantes aux professionnels de la maintenance industrielle, l’Association française des ingénieurs et responsables de maintenance (Afim) a conclu un partenariat avec RS France, leader de la distribution de solutions pour les industriels. Cette collaboration a pour objectif de faciliter l’accès à l’ensemble des solutions […]
Quand un assistant en réalité augmentée veut révolutionner la maintenance et le dépannage industriels
Transformer la gestion des données en temps réel en une expérience immersive. Voici l’ambition de la nouvelle application Sara de Sick. Disponible sur smartphone et tablette, celle-ci permet aux techniciens de visualiser les données de diagnostic et de surveillance directement sur les équipements. Cette solution intuitive aide à réduire les temps d’arrêt, facilite le dépannage, […]
La maintenance face aux Enjeux de la RSE : une journée de conférences le 24 octobre
Le département de Génie Industriel et Maintenance de l’IUT Louis Pasteur de Schiltigheim (Université de Strasbourg) en collaboration avec l’Association française des ingénieurs et responsables de maintenance (AFIM), organise le 24 octobre prochain à partir de 9 heures une journée en direct dans le cadre d’Innova Maintenance. La RSE et son impact sur la maintenance industrielle est un sujet qui explore […]