Électrification des fours industriels : une étude identifie les freins et les solutions afin d’aider à décarboner l’industrie française
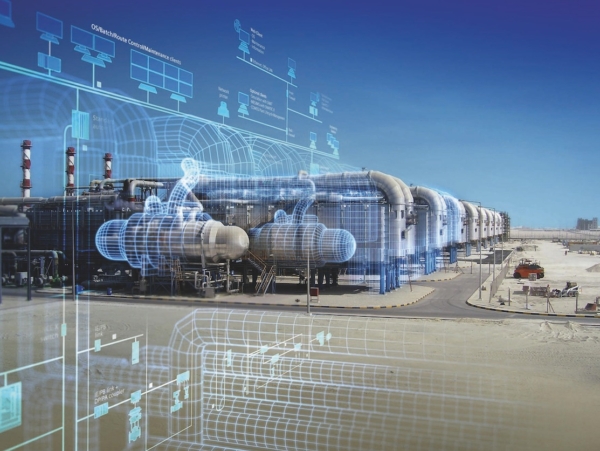
Dans un contexte de réduction des émissions françaises de gaz à effet de serre, Colombus Consulting, cabinet de conseil en management, publie une étude consacrée à l’électrification des fours industriels.
Les fours industriels représentent 60% de la consommation d’énergie de chauffage industriel et 90% de l’énergie consommée par ces activités provient de combustibles fossiles : décarboner leur utilisation est donc un levier climatique majeur.
Les fours industriels sont principalement utilisés dans cinq secteurs en France : la sidérurgie, la chimie de base et l’industrie pharmaceutique, les minéraux non-métalliques, la métallurgie et l’agroalimentaire. Pour répondre aux objectifs de décarbonation de ces secteurs, le nombre de fours électriques devrait doubler ou tripler d’ici 2035, tout comme la consommation en électricité liée à l’utilisation de fours.
L’électrification des fours industriels : enjeu primordial pour réduire les émissions françaises de gaz à effet de serre
L’industrie française représente 20% des émissions nationales de CO2, les fours industriels consomment chaque année 155 TWh d’énergie, en quasi-totalité d’origine fossile : décarboner les 155 TWh consommés par les fours industriels serait un puissant levier climatique pour la France. 60% de l’énergie finale consommée par le chauffage industriel l’est par des fours industriels, qui fonctionnent aujourd’hui très majoritairement aux énergies fossiles.
Les fours industriels sont principalement utilisés dans cinq secteurs en France : la sidérurgie, la chimie de base et l’industrie pharmaceutique, les minéraux non- métalliques, la métallurgie et l’agroalimentaire. Ils utilisent principalement le gaz naturel mais peuvent également fonctionner au coke ou au fioul.
Afin de répondre aux objectifs de décarbonation de ces secteurs, le nombre de fours électriques devrait doubler ou tripler d’ici 2035, tout comme la consommation en électricité liée à l’utilisation de fours. Ce potentiel d’électrification est présent et peut être atteint.
De nombreux acteurs nationaux pourraient participer à la décarbonation du chauffage industriel. La France possède des leaders mondiaux pour les fours industriels, bénéficie d’une balance extérieure bénéficiaire de plus de 90 millions d’euros chaque année et exporte en grande partie des fours électriques. Exportatrice de fours industriels, en particulier de fours électriques, elle aurait ainsi tout intérêt à miser sur cet écosystème industriel local pour décarboner son industrie.
De nombreuses solutions d’électrification existent
L’étude Colombus Consulting révèle plusieurs freins à l’électrification des fours : coût d’investissement parfois élevé, nécessité d’adapter le raccordement à la haute demande en électricité, manque de recul sur certaines technologies pour d’autres secteurs (fours à conduction ou hybrides), spécificité de certaines technologies à induction, et, surtout, blocages normatifs liés au changement de processus que doivent gérer clients.
« L’électrification des fours est freinée par deux facteurs majeurs : l’éventuelle nécessité de re-certifier le processus et les coûts d’investissement élevés. L’électrification des procédés fait aussi remonter un enjeu de raccordement du réseau et de manque de maturité de certaines technologies pour des secteurs particuliers, comme la verrerie », indique Nicolas Goldberg, Senior Manager chez Colombus Consulting
En revanche, l’étude identifie et met ainsi en évidence plusieurs leviers d’électrification. De nombreuses technologies sont en effet déjà disponibles : fours à résistances électriques, fours à induction, fours à arc électrique, fours à conduction, etc.
Le recours aux mini-aciéries, modèle largement utilisé aux États-Unis, permet d’électrifier le secteur sidérurgique tout en encourageant l’économie circulaire avec le recyclage de fonte.
Par ailleurs, le renforcement de mesures incitatives permettraient d’électrifier plus largement l’industrie française. Le renforcement des aides et subventions proposées aux fournisseurs et aux utilisateurs de fours électriques vont aider à développer certaines technologies pour en faciliter l’utilisation et en réduire les coûts, tout en motivant les clients à entamer des procédures parfois fastidieuses mais nécessaires au passage à l’électrique. Enfin, le développement des investissements en R&D pour la certification des technologies électriques lèverait le frein majeur de la requalification des procédés.
Le nouveau numéro de Production Maintenance va bientôt paraître !
Chers lecteurs et internautes, Le n°90 de Production Maintenance va bientôt paraître. Comme à son habitude, le magazine leader en France dans le domaine de la maintenance industrielle va mettre en lumière de nombreuses innovations technologiques, des bonnes pratiques afin d’aider les professionnels de l’industrie à optimiser la surveillance et la disponibilité de leur outil […]
Rennes Métropole inaugure le Bâtiment 78, coeur du Pôle d’excellence industrielle à La Janais
Avec le soutien de l’État et de la Région via le Contrat métropolitaine de relance et de transition écologique, la Métropole a opéré la réhabilitation d’un bâtiment industriel dit « Bâtiment 78 », acquis par Rennes Métropole auprès du groupe Stellantis, en vue d’y réaliser un équipement emblématique du PEI avec comme fonctions principales : l’accueil de […]
Découvrez notre gamme de joints toriques et bagues BS pour une étanchéité optimale
Conçues pour les applications industrielles, nos solutions d’étanchéité Hutchinson offrent performance et durabilité, même dans des environnements très exigeants. Fabriquées à partir de matériaux de haute qualité, nos pièces résistent aux températures extrêmes, produits chimiques agressifs et à l’usure mécanique. En savoir plus